Featured for
Licence info tool
Learn what licence is required for different types of building and construction work.
Retention trust training
Trustees are no longer required to complete retention trust training.
Image
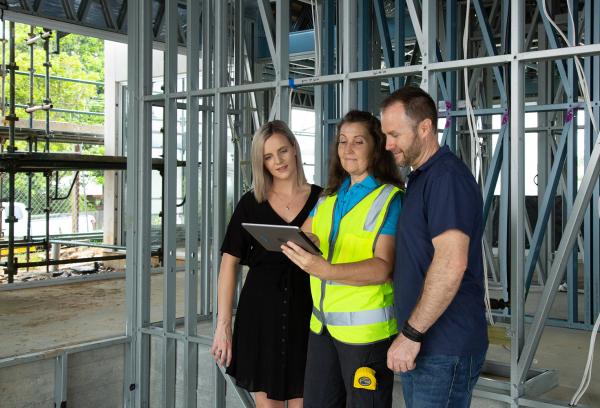
Home owners: check out the Home Owner Hub
A home is one of the biggest investments you will ever make. We're here to help things run as smoothly as possible.